
3 Strategies for Office-to-Lab Conversions
Following an aggressive growth period of funding for therapeutic discoveries and development fueled by the pandemic, the life sciences market is normalizing to pre-pandemic levels. Nonetheless, it is projected to continue to grow in its original trajectory with continued emphasis on speed-to-market. However, developers today are now more strategic in their future investments, and many are looking at office-to-lab conversations as a cost-effective strategy to expand their life science real estate. They require expertise and knowledge of the market conditions to effectively repurpose space. Realising no two life science markets are the same and that space requirements for research and development vary immensely, this article highlights three strategies that can help make the office-to-lab real estate conversions a success, no matter the location.
1. Know the Industry, Know the Growth Trajectory
Utilising all intelligence available to understand the current market and the business goals of potential tenants gives both the owner and the design team a clearer picture of what the renovated space needs to offer. Typically, companies focused on similar kinds of research are centered around industry clusters in metropolitan areas. Understanding the scientific and economic drivers of the industry that a cluster supports, along with the growth trajectory of companies in the industry, will inform the type of tenant that is likely to be interested in available real estate.
For example, the following industry clusters have been identified in the United States:
- Cell gene therapy companies continue to drive demand in the Raleigh Durham (including Research Triangle Park) industry cluster1
- Incubator space continues to grow in Philadelphia2
- Big Pharma is highly active in the San Francisco Bay Area and is increasing scale in the gene therapy biomanufacturing space3
- NIH funding spurs the life science markets in the Northeast corridor – from Boston and Cambridge to Washington, D.C., and Baltimore2
In addition to geographical industry trends, it’s important to understand growth trajectory and how that relates to space needs. Biotech and advanced life sciences companies move through a sequence of growth phases with different space requirements based on the stage of research, source of funding, and need for ancillary office and/or manufacturing space. In a 2019 report, ResGroup and CBRE4 broke growth stages down into the following:
- Start-ups: Often incubators to maximise R&D dollars
- Graduate: Focused on basic research/drug discovery, prototyping, and typically in the pre-clinical trial stage
- Mid-Size: Typically in clinical trial stages I-III and focused on beta and preliminary market product testing
- Mature: Focused on publishing clinical results, regulatory review/approval, and initial market launch
- Scaling/Expanding: Post-market clinical studies, IPO/Potential M&A
The report then broke down spatial requirements for each stage. Below, we’ve created a matrix of key considerations for each stage, taking into account both ResGroup and CBRE findings and our experience working with different clients:
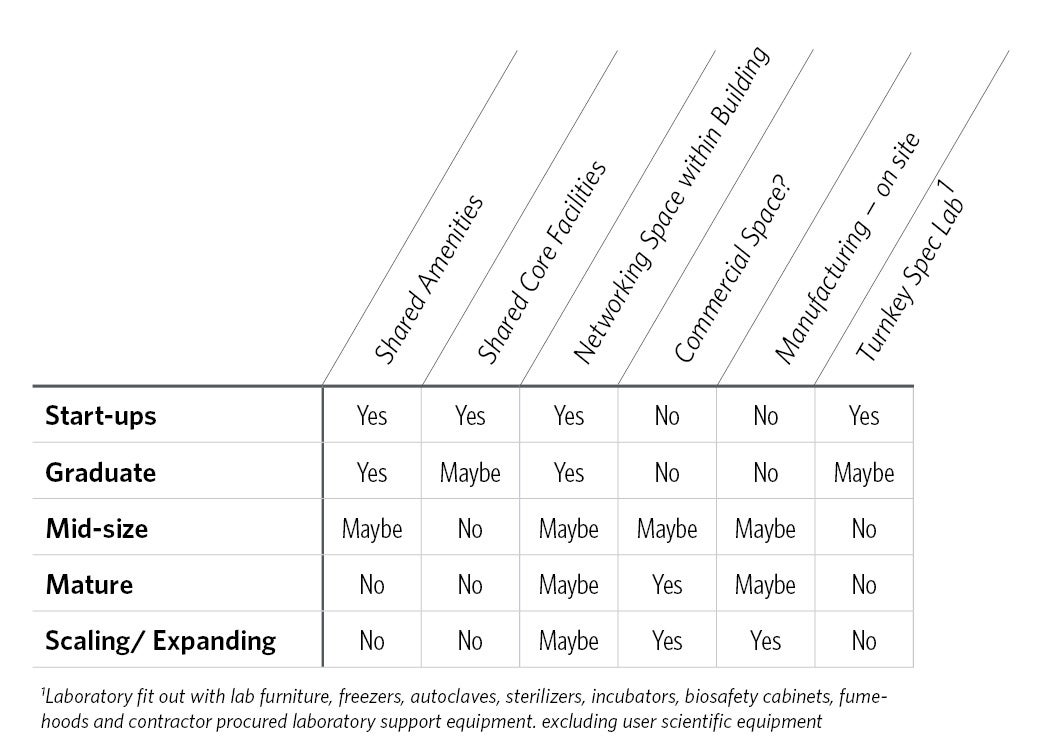
2. Develop a Clear Tenant vs. Developer Scope Matrix
Planning the capital costs for life science development should include budget allocations for both the developer and the tenant. Typically, project briefs for tenant projects are a mile wide but only an inch deep, lacking a detailed scope identification between developer and tenant. The developer should partner with a design team that has a sound understanding of science facility planning to help identify the scope delineation for building elements. Market research teams should study the opportunities for flexibility to accommodate growth based on tenant needs. Lab planning experts can help develop laboratory planning strategies and typologies that offer flexible templates for life science spaces.
For example, the developer can upgrade base building utility capacity for a nonspecific tenant typology assuming a percentage mix of office, wet and dry laboratory with standard utility, electrical and mechanical capacities. Unique exhaust or utility upgrades for specific tenants can be borne at cost by the tenant. Every project is different, but regional trends will often prevail in the delineation between what the owner offers vs. what the tenant is willing to pay as part of a facility for their research space. The growth phase of the company can also drive tenant preferences. Usually, start-ups prefer to occupy fit-out laboratory space that can serve their needs and avoid diverting capital funding toward laboratory furniture and laboratory support equipment.
3. Identify Opportunities and Limitations in Existing Space
Outfitting tenant spaces in commercial office buildings for life science research purposes cannot be accomplished with a cookie-cutter approach. Below are five strategies that the owner and design team should consider when developing plans for the space.
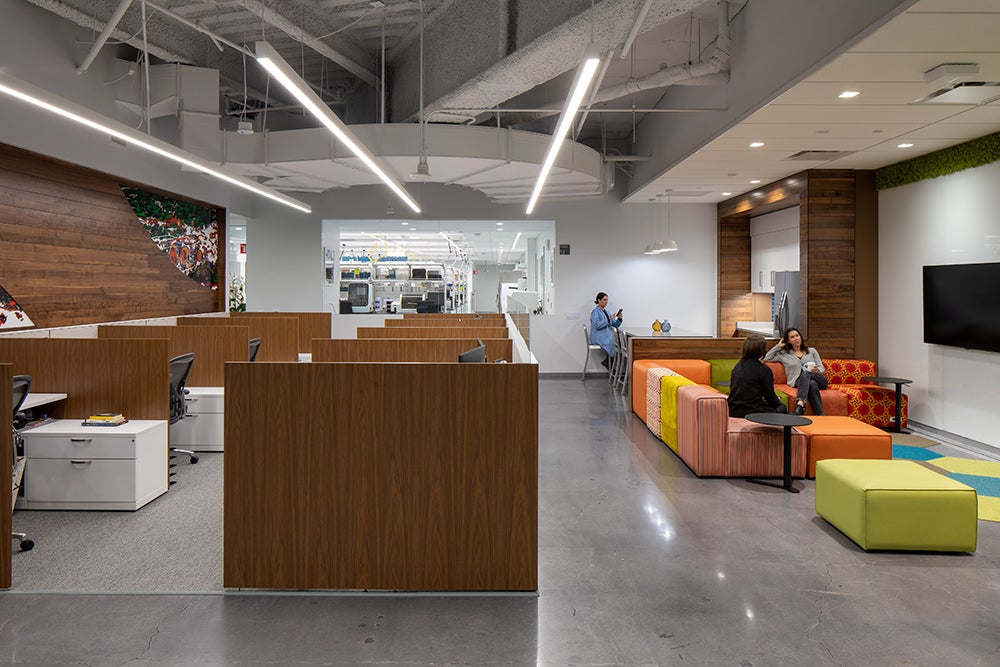
Optimising the Grid
At a building arrangement level, laboratories should be grouped by their space-type category connected by circulation routes. Their arrangement should be informed by its adjacency to office areas and the location of shafts, elevators, and staircases. Preliminary grouping arrangements should consider column spacing of the existing floor plate which influences program arrangement and tenant divisions.
Existing column spacing should be analysed to develop a grid that allows flexibility in arranging various laboratory functions. Typical laboratory module bays range from 10'-8" for open bay light chemistry/biology to 12' for closed laboratory support spaces with freezers, incubators, fume hoods, or high-density cold storage.
Once the grid is understood, a modular lab scheme can be developed. Shared and rentable laboratory support spaces can be planned for buildings with multiple tenants to drive for low rental costs. However, a modular layout that facilitates lab suites ranging from open and shared to dedicated laboratory space allows flexibility in addressing the intellectual property concerns of tenants and accommodates the desire for expansion when companies secure additional funding.
Maximising Space
Grouping laboratory support spaces can help to bridge the limitations of the floor-to-floor height of office buildings. Typical office buildings tend to have smaller mechanical rooms and shallower ceiling spaces and vertical shafts, while laboratories typically have ceiling heights of 13' to 15.’ Some larger tenants expect 15-18' clear heights to accommodate scientific platforms with higher HVAC demand with dedicated distribution and power systems. Increased duct sizes can be accommodated within existing floor heights by planning laboratory support rooms with high service demands along low ceiling zones towards the interior.
For high-rise buildings, a paradox exists in the placement of laboratories on higher floors. Shaft sizes agglomerate from lower floors to higher floors, reducing the net available floor space for the program on higher floors. Placing laboratories on higher floors mitigates the loss of net area and permits the ease of exhausting toxic and contaminated exhaust from the laboratories. However, floor loading requirements also increase as one moves up in a building. The increased structural floor loading for the above mechanical and electrical requirements typically requires the laboratory to be designed for 120-150 pounds per square foot compared to 80-100 pounds per square foot for office spaces. Additionally, most building codes limit the quantities of hazardous chemicals allowed the higher you go up in a building. Developers should evaluate options using a cost-benefit analysis to decide the placement of laboratories in high-rise buildings.
Reducing Energy Usage
Due to high energy demands, meeting energy targets is a challenge in laboratories. It is essential to review the municipal regulatory requirements for energy efficiency in conversion projects to ensure the building can stay below the energy consumption targets per the permit application while also complying with the sustainability goals for the project. Grouping laboratory functions and types based on service demands and their location of placement within a floor can have a major impact on reducing energy usage intensity (EUI) by reducing external environmental factors. Whole building energy simulation is the most comprehensive way to quantify and account for the savings, and hence energy modelling is crucial for such projects.
Making Room for Amenities
Amenity space is analogous to an “interstitium,” where it offers a connecting link in a building between science teams like the interstitium does in biological systems. Plenty of anecdotal evidence exists of the serendipitous exchange of ideas leading to scientific discoveries. Companies often use these spaces for community building and fostering collaboration. Amenities may include spaces for a gymnasium, yoga/pilates rooms, meditation rooms, cafes, and a cafeteria. Offering high-quality amenity spaces such as terraces or atriums can help compete for tenants by offering the types of spaces that attract employees. Based on the tenant mix, amenity spaces can be designated on a floor or interspersed on various floors, depending on the building form. Design teams can ideate multiple massing options to help arrive at a decision early in using the building massing/blocking to maximize utilisation of the land parcel's buildability potential.
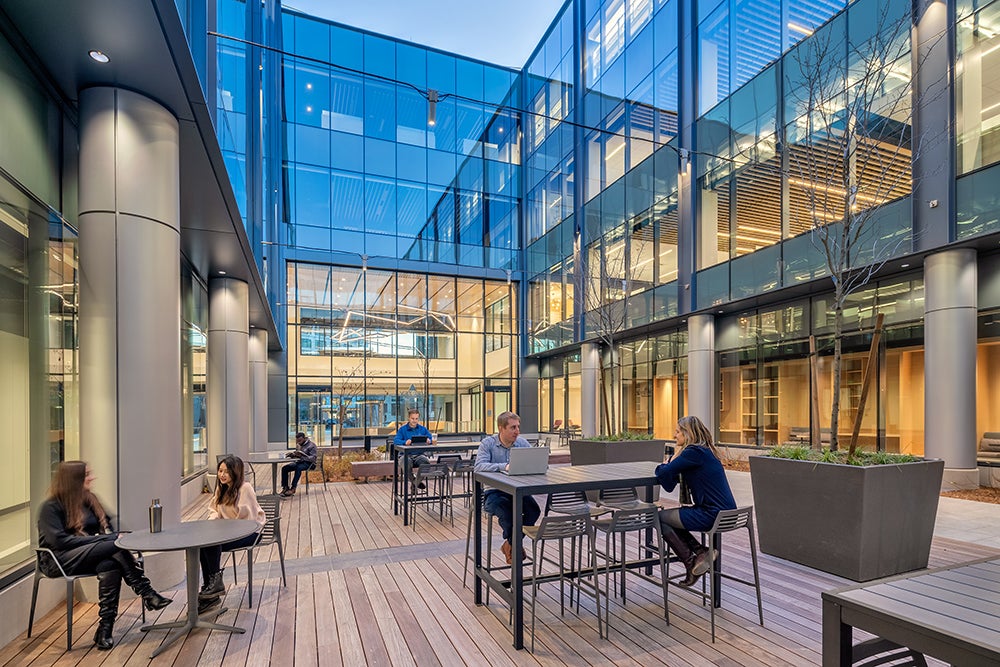
Assuring Code Compliance
Life science research laboratories that carry out experiments with biological, chemical, or radiological material are required to meet provincial, federal, and local regulations, guidelines, and safety standards. Options exist to designate office occupancy for laboratories if designated areas can be designed as control areas or hazardous zones with required fire barriers and safety devices. Designated occupancy classification could broadly range from office occupancy with control areas and low-hazard occupancy to high-hazard, depending on the type of laboratory hazards. The laboratory area needs to be designated with appropriate fire separations for control areas for the permitted quantity of chemicals, flammable, and gases. It can be particularly helpful to get design professionals involved with assessing the flammable and chemical use of the planned research activities and verify quantity stored and used meets regulations, particularly higher up in the building. e.g., Per CBC 2019, for Business (B) occupancy above seven stories, only 5% of allowable flammable chemicals are permitted in a maximum of two control areas, while above ten stories, only one control area with 5% is permitted.
Accommodating large laboratory tenants may require rezoning, which may require a variance to previously issued development permits. Some municipalities have specific restrictions on laboratory types close to residential neighbourhoods. For example, in the city of Berkeley, biological containment level 3 laboratories are not permitted in Mixed Use light Industrial District Zoning and containment level 2 laboratories are not permitted within 500 feet of Mixed Use Residential District Zoning.
Other design issues to consider include:
- Stringent vibration and shielding requirements based on instrumentation within the lab. Typical laboratory floor vibration criteria range between 4000 µinch/sec to 2000 µinch/sec for stringent vibration needs. Note that the lower range of 4000-2000 costs a significant premium and should be considered for select areas only (2-3 bays max) centrally located on the floor as defined in the matrix/lease.
- Vertical circulation to support incoming laboratory materials and outgoing waste should be analyzed for size, quantity, and location to facilitate access to tenant spaces. Laboratories may need larger freight elevators or even dedicated ones for lab use only.
- Service loading and dock for bringing in consumables, storage, and supply of chemicals and research materials, and move-in/installation of large equipment. Separation of outgoing waste flow and used consumables from routine functions in the loading dock is an issue of vital importance.
Looking Ahead
As top life science investors continue to make plans for major real estate investment, informed decision-making will be key to long term sustainability. The developer community should use this opportunity to create flexible, adaptable research spaces that will be responsive to trends related to funding, partnerships, and research priorities over time. While the conversion of an existing office building to a life science research space is complex, most hurdles can be overcome when collaborating with a design team that has expertise in science facilities.
References
- NC’s life science sector lands $2.1B in expansions plus 2,700 job commitments in ’22
- Greater Philadelphia Life Sciences Incubators Cheat Sheet for Entrepreneurs
- Life Sciences 2.0: How San Francisco Could Bounce Back With a Biotech Boost
- Market Assessment of Life Sciences Laboratory Space in Philadelphia