
Experts Talk: Accelerated Bridge Construction with Nick Burdette
Experts Talk is an interview series with technical leaders from across our transportation program.
Applying the techniques used in accelerated bridge construction to some or all structural members can expand design possibilities while safely accelerating delivery.

A native of Philadelphia, Senior Bridge Engineer Nick Burdette entered the industry in the United Kingdom before joining our Pittsburgh office 10 years ago.
He has deployed accelerated bridge construction techniques on a wide range of structural components — some very large — for a variety of notable bridges. Among them are the Gov. Mario M. Cuomo (New NY) Bridge in New York, and the Marc Basnight Bridge (Bonner Bridge Replacement) in Outer Banks, North Carolina.
Accelerated Bridge Construction
Q. You’re meeting with an agency that needs multiple bridges replaced in a short time frame. It sounds like a good project for using accelerated bridge construction. How do you describe ABC to the agency director?
A. Accelerated bridge construction sounds like a good fit for this project if the most important element for you is speed of construction in the field. Perhaps these project bridges involve busy interstates or tollways, active rail lines, or provide the only access to critical sites. We can figure out how to replace your bridges very quickly, perhaps in as little as a weekend. To do this, we will either build the replacement bridge nearby and slide or roll it into place, or we’ll prefabricate the replacement structure in pieces that can quickly be connected on site to reduce construction time for the new bridge. Let’s look at how quickly you need these bridges replaced and get started on some options!
Q. How will the use of ABC impact project outcomes?
A. The biggest impact is reduced field construction time affecting the users of the bridge.
For the right situation, accelerating construction to reduce user impacts can have significant economic benefits. Economic models showing the dollar-cost of transportation delays and impacts have become more sophisticated, and it is possible to quantify the regional economic impact of a bridge closure. For some sites, ABC makes economic sense.
The second major impact of ABC is positive public relations. People are concerned with projects that impact their mobility. When a transportation agency shows that it’s willing to innovate to deliver quality projects that reduce public impact, communities feel they are being heard and trust is built as well as the bridge.
The third benefit of ABC is that it shortens the duration that construction workers are exposed to the dangers of field conditions. While construction safety has improved significantly, risk of accidents is still greatest when working on a bridge site with active traffic. Accelerated bridge construction offers safety benefits by completing much of the work off-site and away from traffic.
Q. What conditions should be met before considering the application of ABC?
A. The main condition that should cause owners to consider ABC is when there is a high cost to bridge users from construction traffic impacts. Bridges on or over major interstates or tollways, active rail lines, or structures that provide critical access to business, hospitals or emergency services can be good candidates. Large, repetitive structures are also great candidates for ABC, as the cost of design and off-site custom fabrication can be spread over many repetitive elements for a net cost savings. Precast concrete pieces are a primary element of most ABC bridges, and precasters produce these custom elements economically through repetition. One important point to remember is that ABC does not mean accelerated bridge design. The design and fabrication schedule should be extended beyond that of traditional design, likely meaning more time before crews first break ground at the bridge site. This design time is critical to ensure that the complex elements and procedures needed to rapidly replace the structure are fully developed and ready for field execution.
Q. What are the most popular methods of accelerated bridge construction, and why?
A. Popular ABC methods include sliding or transporting a completed new structure in into place, or prefabrication of the replacement structure in pieces that can quickly be connected on site. Where space permits, a common technique is building the new bridge on temporary piers next to the bridge planned for replacement. In a short closure (with crews working continuously), the existing bridge can be demolished and the new one slid into place on rails with pads or rollers. Transporting a bridge into place follows a similar process to sliding, but uses self-propelled modular transporters on dozens of synchronized tires to “drive” a completed structure into place. Both of these methods can be extremely fast, permitting replacement of a bridge span in a night closure, but they require specialized equipment and experience.
Probably the most popular ABC technique is prefabrication of the replacement structure in modular pieces. With good design and extensive planning and pre-work, these pieces can be connected with bolts or fast-curing concrete to create a finished bridge structure very quickly. Durations for this technique can range from days to months, depending on the size of structure and extents of prefabrication.
Q. Describe projects you’ve worked on where ABC improved an outcome for the client or community?
A. I’d like to highlight three recent bridge projects.
Bonner Bridge Replacement
The first is the Marc Basnight Bridge (Bonner Bridge Replacement) in the outer banks of North Carolina. This new bridge is nearly 3 miles long and crosses the Oregon Inlet between the Pamlico Sound and the Atlantic Ocean. Due to the harsh marine environment, our team proposed extensive use of precast concrete elements, many of which are post-tensioned, so they can quickly be assembled like LEGO blocks. Positive outcomes for this ABC technique stem from moving much of the construction work to the controlled environment and safety of a precasting yard: improved quality and reduced construction time in dangerous conditions.
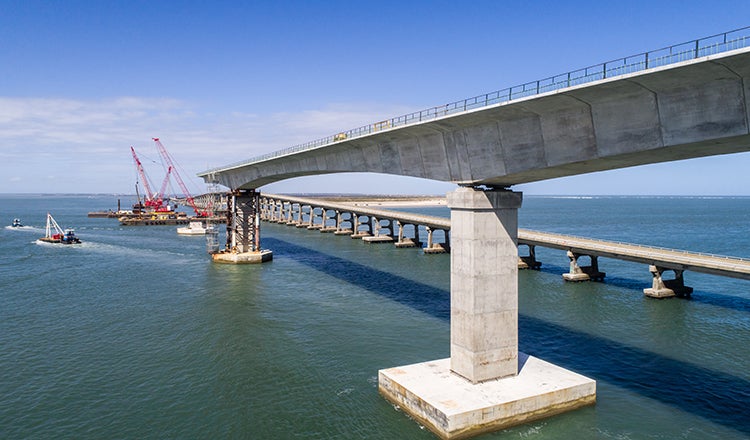
Gov. Mario M. Cuomo Bridge
The second project is the Gov. Mario M. Cuomo Bridge (Tappan Zee Bridge replacement). For this structure, design of nearly 60 approach piers was standardized to permit the use of precast concrete “tubs” for the waterline footings and pier caps. Some of these concrete tubs were a story high and the size of a tennis court. They were fabricated off-site and later lifted into place using one of the largest derrick barge cranes in the world. ABC prefabrication of these tubs as well as large sections of the steel approach superstructure helped the contractor keep to an aggressive construction schedule. Construction could proceed simultaneously on site and in prefabrication yards across the country, accelerating completion and opening of the first replacement bridge.
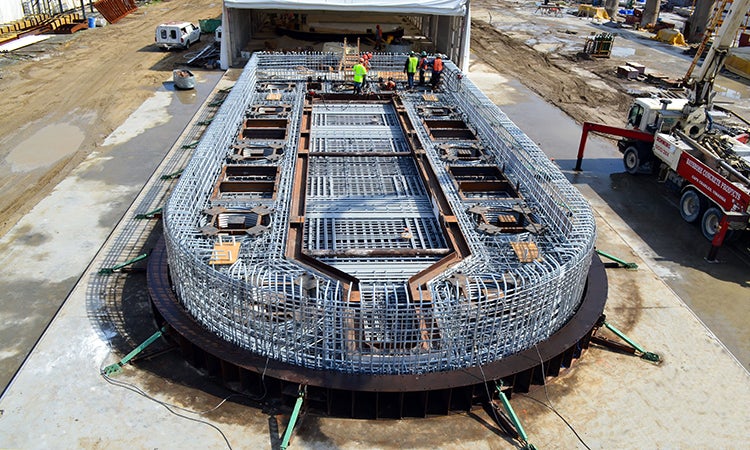
Pennsylvania Rapid Bridge Replacement
The third project to highlight was not a huge bridge, but rather replacement of 558 little ones. The Pennsylvania Rapid Bridge Replacement project is a public-private partnership to replace 558 structurally deficient bridges in Pennsylvania. As part of this project, the state DOT designated some critical sites for rapid replacement — with only two- or five-week closures permitted. The client selected these sites for ABC for many reasons, including limiting impact to emergency medical services.
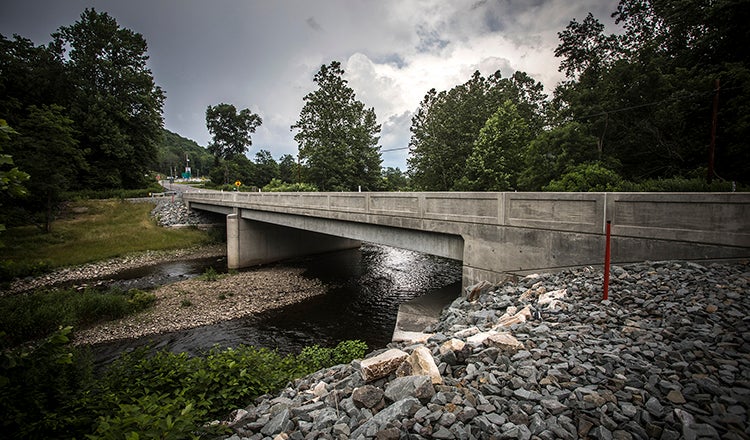
Inspiration & Advice: Nick Burdette
Q. What inspired you to become a bridge engineer?
A. I grew up in Philadelphia, and every summer we would cross the Delaware River on our way to vacation at the beach. I remember being ten years old, in the back of my families’ purple mini-van, crossing the Ben Franklin Bridge. At ten, this was as close to flying as I had ever been. I watched the sun on the water and boats on the river far below. I looked up at the enormous suspension cables, and they seemed to hang from the sky. That’s when I knew I wanted to make bridges.
Q. What advice do you have for bridge designers who are new to the profession?
A. Get out on a construction site and see how bridges are built. Bridge design is much more than just choosing proportions to resist applied loads. It requires careful consideration of how the structure will be built, what constraints will affect the design, and access methods a contractor might use. I had the good fortune to spend a year early in my career as a field engineer on a bridge site, and I often come back to lessons learned that year. In other countries, such as the UK and Australia, a year in construction is required as part of professional licensure. It is an extremely valuable experience to seek out as a young designer.
Each Experts Talk interview illuminates a different aspect of transportation infrastructure planning, design and delivery. Check back regularly to gain insights from specialized experts and thought leaders behind our award-winning, full service consulting practice.