
Experts Talk: Navigating Modern Design-Build Projects with Jay Chiglo
Experts Talk is an interview series with technical leaders from across our transportation program.
Exploring the Promise of Progressive Design-Build and Other Trends in Effective Project Delivery
Over the last few decades, design-build has rapidly become popular in transportation infrastructure, celebrated for what the delivery method’s supporters champion as its ability to complete projects much faster than a traditional design-bid-build approach. But the increasing adoption of the delivery method has also led to some significant growing pains. While many projects are completed successfully, the 2022 Design-Build State of Practice report by the American Council of Engineering Companies noted that “the majority (56%) of large projects experienced claims, disputes and/or litigation.” In response to this marked increase in disputes, many in the industry are reassessing their use of fixed-price design-build and taking a closer look at the benefits of the progressive design-build method.
Jay Chiglo coordinates the development of our alternative delivery transportation projects globally, including design-build, public-private partnerships and more. Jay has been responsible for the successful management, oversight and delivery of some of the largest and most complicated transportation projects that HDR has designed. He is also well known and active in various industry associations, including the Design-Build Institute of America, American Council of Engineering Companies, Associated General Contractors and more. In this interview, he discusses recent challenges with traditional fixed-price design-build, the promise of progressive design-build and what the industry can expect in the next 5-10 years.
Q. How has the design-build environment changed in recent years?
A. It was about 10 years or so ago that the industry really started to see more challenges, especially on megaprojects. A year or two after these megaprojects were awarded, contractual issues would arise from either a schedule or financial perspective. As the contractual issues surfaced, claims quickly followed, affecting nearly every party involved, including owners, design-builders, concessionaires, design-builder joint venture partners and designers.
Many of the recent difficulties come down to the risks assigned to each party. In recent years, owners began shifting risks they had traditionally taken on, like unforeseen site conditions, property acquisitions or coordination with third parties. The design-build team priced those risks with only preliminary information, despite the projects being early in the design process. That shifting of risk led to many unforeseen schedule and financial challenges. And the resulting complications have prompted many contractors to decide they’re no longer going to pursue fixed price design-build opportunities at all because of the financial impacts they have incurred under this approach.
The current environment, with fewer contractors interested in design-build projects, has created new challenges for owners. When projects are put out for procurement with limited interest, it causes delays. We’ve seen projects put on hold or programs that needed to be divided into smaller phases because of a lack of interest in large DB projects. If agencies prepare their whole procurement with one approach in mind and then discover at a late date that they need to change their procurement method, that’s not a fast switch. The larger the project, the worse it is from a schedule standpoint. And then because of the delay in the schedule, everything can snowball. What used to be a CA$1 billion project may quickly become a CA$1.3 billion project. That can lead in turn to funding issues, and the challenges continue.
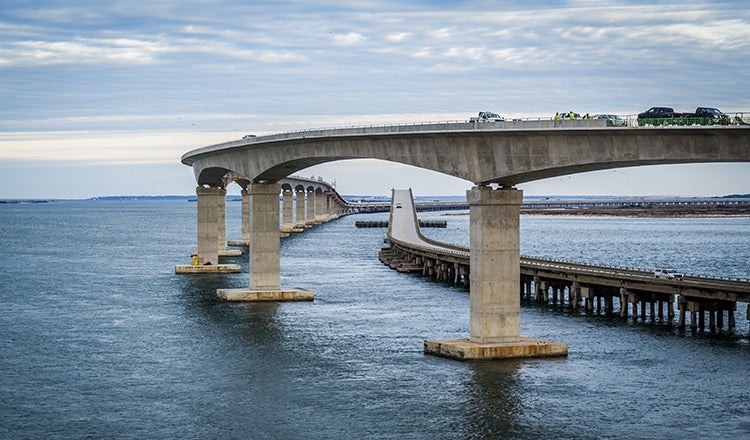
Q. Why is the industry paying much more attention to progressive design-build?
A. The progressive design-build method introduces a number of refinements. The biggest is the level of design completion before the design-build team submits their pricing. In a traditional design-build, the design-build team receives limited design information from the owner and, while still in the pursuit stage, is required to advance the design, at its cost and risk, to a level that is roughly to the 15-30% level of design. In a progressive design-build, the design-build team is selected on a qualifications or best value basis. The owner and the selected design-builder then begin “phase 1” of the agreement whereby the design is advanced, in collaboration with the owner, to the point that the design-builder is comfortable with negotiating a final scope, schedule and price for the project. This is typically to at least the 60% level of design.
The significant differences from traditional or fixed-price design-build are that the owner is collaborating in the design development process and the design-builder is being compensated for the phase 1 services. The project moves to phase 2 final design and construction upon final agreement on scope, schedule and price. As the design is collaboratively advanced during phase 1, the teams can work through a lot of the design issues, staging issues, third-party issues and technical concerns with an owner. The owner has greater involvement during this phase than a traditional design-build project. For instance, if there's a geotechnical concern, parties can perform more investigation upfront, so they have a better understanding of the design parameters that are needed to advance the preliminary design before pricing the whole project. This provides better certainty and less risk so design-builders can prepare more accurate estimates and carry less contingency.
Another advantage of the collaborative approach of progressive design-build is price negotiations. There are times when the owner thinks an element of the project should cost X, the contractor thinks it will cost Y, and there's a big discrepancy between the two. The progressive model allows the parties to work together to resolve the pricing discrepancy. This results in a better project understanding and more accurate and fair pricing. In many cases, that collaboration hasn’t happened in traditional design-build.
Progressive design-build is catching on quickly in states that are using it, such as Florida, Utah, Kansas and elsewhere. One major challenge is that many state departments of transportation are required to select contractors on a low-bid basis, rather than the qualifications-based process that progressive design-build employs. In these states, legislative approval is often necessary to authorize the new delivery method.
Some observers raise the concern that progressive design-build may cost more than design-build, but that observation often only compares the initial cost estimate, which does not reflect the final cost after change orders, claims and such. So far, it appears that a progressive approach has fewer challenges that lead to cost escalations and delay during the project.

Q. How is the professional liability insurance market being affected?
A. As claims and litigation have increased on design-build projects, the cost of insurance for professional liability coverage has increased substantially. Particularly on large projects, the cost of project-specific professional liability policies has skyrocketed in recent years and availability has shrunk. Some insurers that formerly provided these PSPL policies now won’t issue them at all for design-build projects because of higher claims activity. In general, this increase in premiums is attributed to fixed-price commitments made early in the project design process and risk allocations that fall more heavily on the design-builder (which often then leads to more claims).
There’s optimism that progressive design-build may alleviate many of these concerns, but as this procurement type is still somewhat new to transportation infrastructure, many insurers are watching closely to see how early projects are completed and whether there will be a substantial reduction in professional liability claims.
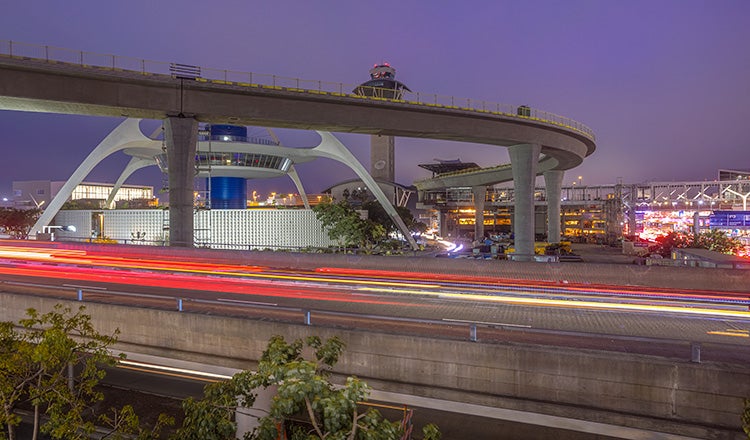
Q. What makes projects better suited for design-build, progressive design-build or a different delivery method? What factors should play into the decision to use a particular approach?
A. I was at a presentation recently with a state DOT and counties from the state, and I was asked what my preferred delivery method would be. Somewhat to their surprise, I said design-bid-build. We’ve been using it more than 100 years, and we know it works. If it’s a straightforward project and schedule isn’t an issue, design-bid-build continues to be a great option. It’s when schedule, complicated staging, maintenance of traffic or other innovation is important that alternative delivery methods can help lead to a successful project.
When it comes to these alternative delivery methods, choosing the right option for a project or program largely depends on the owner and how comfortable they are with different procurement alternatives. But there are some general guidelines that can inform decisions. If a project is pretty straightforward technically and there’s not a lot of third-party risks, design-build is still a good option for completing a project on an accelerated schedule.
If a project has very complicated maintenance of traffic issues, complex staging or many third-party issues, it might lend itself more to a progressive approach, where those complications and their associated risks can be thoroughly discussed and all parties can participate in the development of the right solution. In De Soto, Kansas, for instance, we’re assisting the Kansas Department of Transportation in the delivery of its first progressive design-build project, a new 4-mile roadway that was needed on an extremely aggressive schedule (6 months for procurement, 6 months for design and 18 months for construction). Because of schedule needs and significant utility conflicts, a collaborative progressive approach was pursued, and the project is on track to open portions of the project in mid-2024 with substantial completion by the end of 2024, meeting its goal of significant completion within two years of NTP for design.
Another option is construction manager/general contractor, or CM/GC. CM/GC (also referred to in some jurisdictions as construction manager at risk, or CMAR, is similar to a progressive design-build in that it incorporates early contractor involvement and uses a collaborative design process to reach a negotiated guaranteed minimum price. The main difference between the two methods is the number of contracts. In a progressive design-build, there is one contract with the owner, and the designer is part of the design-build team. In a CM/GC, the designer has a separate contract with the owner as does the contractor. This CM/GC contract structure provides the owner with a little more control over the design, but it also requires more involvement, which can be more taxing depending on the size of the program. Similar to design-bid-build, an owner retains design risk in the CM/GC model. On one large megaproject we’re working on, for instance, there will be dozens of separate bid packages. Using a CM/GC would require the DOT to manage each of those contracts, while a progressive design-build would assign that overall responsibility to single design-builder. Either approach is workable and depends largely on the owner’s comfort level, interest and full commitment to project involvement.
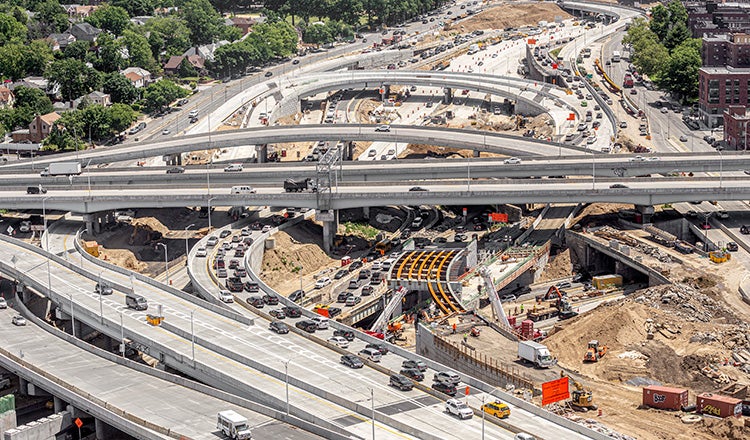
Q. What do you expect to happen in the design-build market in the next 5-10 years? How will projects and approaches change?
A. Looking forward, progressive design-build and its implementation by agencies throughout the United States will be a major theme of the next few years. I think there will be more and more agencies that obtain approval to use progressive design-build as an alternative delivery method. It’s a hot topic right now among transportation officials in the industry, and everybody seems to be watching the projects already in progress to see how they go. But it probably won’t be used in every location, as approving that qualifications-based process requires a level of support among the state’s contracting community and elected officials that isn’t realistic everywhere.
The next few years will also likely see some increasing stability in the PSPL insurance market, as more progressive projects are completed and we see whether there’s a major difference in the claims and litigation between progressive design-build and traditional design-build. If, as expected, there are fewer or smaller claims, hopefully it will be easier and less expensive to secure these important policies and therefore easier to attract more bidders for important megaprojects.
Finally, we should also expect more formalization and consistency in progressive design-build contracts. Right now, each agency is creating its own project delivery guidelines and they’re all a little different. As more projects are completed, we’ll begin to see agencies sharing their best practices and learning from each other to create more consistency across the industry. There are exciting things ahead for the design-build world!
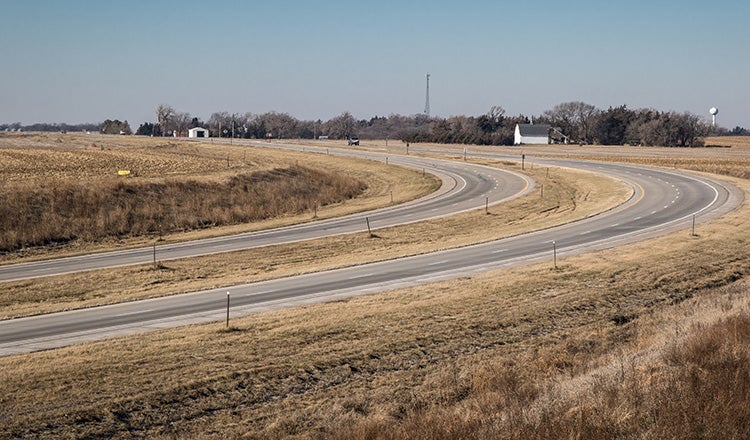
Inspiration & Advice
Q. How did your career lead you to a specialization in alternative delivery?
A. I led my first design-build project back in 2007. I really enjoyed the process and the competitive nature of the procurement. After that effort, I was asked to take leadership roles on other pursuits/projects across the country, which eventually led me to my current position at HDR.
Q. What advice do you have for those interested in pursuing a career in alternative delivery?
A. Reach out to others in your company who are involved with alternative delivery to introduce yourself as they would be a great place to start. More than just being technically capable, you also need to be ready to really understand legal obligations and to faithfully administer contracts. Finally, look for opportunities with industry associations such as ACEC, DBIA, American Road & Transportation Builders Association, etc. to become more involved. These organizations and those involved with them are great places to learn about alternative delivery.
Each Experts Talk interview illuminates a different aspect of transportation infrastructure planning, design and delivery. Check back regularly to discover new insights from the specialized experts and thought leaders behind our award-winning, full service consulting practice.