
Experts Talk: Parametric Bridge Design with Michael Roberts
Experts Talk is an interview series with technical leaders from across our transportation program.
Signature Bridges Become Digitally Alive with Parametric Design
Parametric bridge design is becoming more advanced and is as profoundly different from traditional design as CAD is from drafting with ink on vellum. It forms the critical groundwork needed to support digital design’s transition to the Fourth Industrial Revolution. Parametric design establishes a living workflow that is intelligent, handles intentional and iterative change very efficiently, and helps improve designers’ and owners’ capabilities to see the bigger picture, earlier in the process than in the past. Taking a glimpse into the future of engineering workflows, it applies logic-based, visual programming that dynamically connects design data and geometric relationships to adapt in real-time.

Our Michael Roberts has been developing and using parametric design tools for roughly half of his 21-year structural engineering career. A bridge engineer with a passion for structural design, Michael has a project resume ranging from Olympic ski jumps to the largest self-anchored suspension bridge in the world and a wide range of conventional and signature bridges pushing and flexing the limits of design innovation. In this interview he explains why this approach is so important to the bridge industry in general and signature bridge design in particular.
Q. What do you mean when you say a parametric design model is “intelligent”?
A. In the same way that an Excel spreadsheet updates on input changes, parametric design updates 3D geometry and the supporting engineering analyses, live and in real time. It’s as simple as watching the span of a bridge change in front of your eyes by changing the end point coordinates, yet extremely powerful because of the computational design automation that is connected to those points which automatically updates as the spatial relationships are changed or defined.
The structure isn’t simply visualized — it is designed in a fundamentally different manner that connects two points with more than just a geometric line. We don’t just draw a line, we generate living attributes which are attached to centralized data so that when the geometry shifts, the data recalculates itself — and the digital thread associated with it — allowing us to assess the implications of the change in geometry immediately.
The degree to which this empowers and streamlines design development and decision-making cannot be overstated since we are working with improved data availability in assessing solution viability in the moment. In an environment where design moves fast, adapting to change and keeping up is critical. Parametric design connects the bridge engineer’s expertise and design intent to a centralized digital representation that becomes the evolved proof-of-concept shareable with the team or the owner.
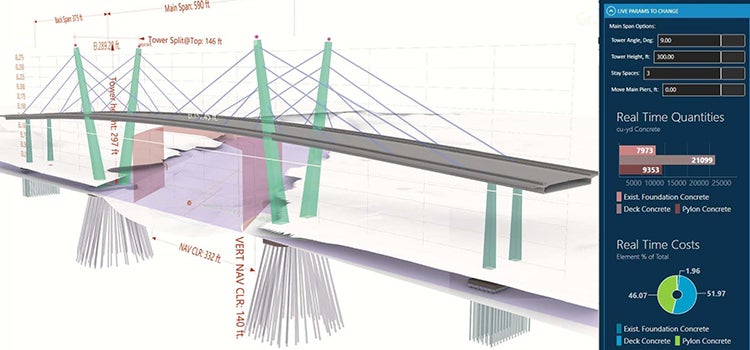
Q. Is this just about using a new, slick piece of software? Isn’t the idea of changing a pier shape having the costs and quantities automatically recalculate too good to be true?
A. This is an understandable concern for any innovative technology, but no different from when we transitioned from manual calculations to spreadsheets. Parametric design tools provide a universal language between designers and their data which streamlines analysis and empowers a design team who’s working with an owner to explore alternatives to articulate a community’s vision for their bridge.
Tools we’re using are compatible across platforms and let an engineer define a parameter (such as a pier dimension) and define rules that act on that parameter to generate the structure’s geometry in an analysis or BIM model. This underlying intelligence means that changes to a parameter automatically recalculate everything from structural support configurations to the quantity of needed rebar. We instantly see implications for constructability, cost, and community impacts so an owner can interact with design ideas and decisions interactively and in real time.
The software we use helps us reduce risk, offer earlier insight, and integrate the client and public earlier with visualizations that are technically accurate and much easier to understand in early stages. The differentiator of parametric design is in how we align these computational tools with our structural engineering expertise to open up collaboration workflows and explore scenarios and solutions.
Q. What’s the most interesting project where you’ve used a parametric design approach?
A. Most recently the Green Street tied arch pedestrian bridge in North Carolina showed parametric design to be pivotal to help the client deliver a better project. Upfront, it allowed us to feel much more confident that the unique arch form was structurally viable heading into a contractual design build agreement. During execution it helped us carry adaptions through the project’s lifecycle — through detailed design and production, to checking field tolerances — to create a precedent-setting workflow that met a limited design and construction budget on an aggressive schedule.
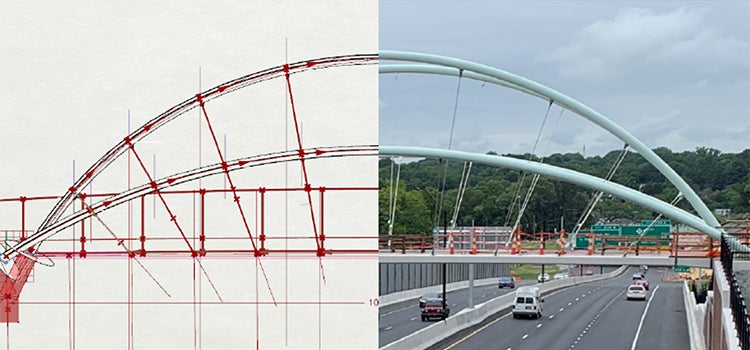
Although final design documents were delivered on paper to the Department of Transportation (not digitally), parametric design was game-changing behind the scenes by enabling a small team to accommodate the complex geometry, changes and unique design challenges efficiently. What was conceptualized during the procurement phase is effectively what’s been built. This demonstrates the proof-of-concepting advantages gained directly from parametric design at the early stages when decisions are paramount and have the greatest impact on a project’s cost. Our approach was key to delivering the aesthetic vision the client and community sought under challenging constraints without deviating from the Request for Proposal.
Q. Does this change how we work with an infrastructure owner or a contractor?
A. It can fundamentally change the usefulness of a discussion with a contractor or owner about how a signature structure might be staged or phased or erected, because seeing is believing. The parametric model allows “what if” discussions during a meeting or a workshop and in front of their eyes. What if you move the base plate five feet to accommodate a clearance or subsurface condition? How does that rework the design and the erection scheme? Does larger reinforcement fit in this shaft and avoid conflicts?
Analyses that sometimes take structural designers weeks to generate, adapt to, or calculate may be accomplished through parametric modeling in minutes instead if initially set up for that purpose. This type of dramatic transformation allows a practical conversation between designer and builder to define construction means and methods for a signature structure. The parametric model becomes the central model for down-stream digital connections, be it Excel data tables for plan sheets, the structural analysis model or the BIM model.
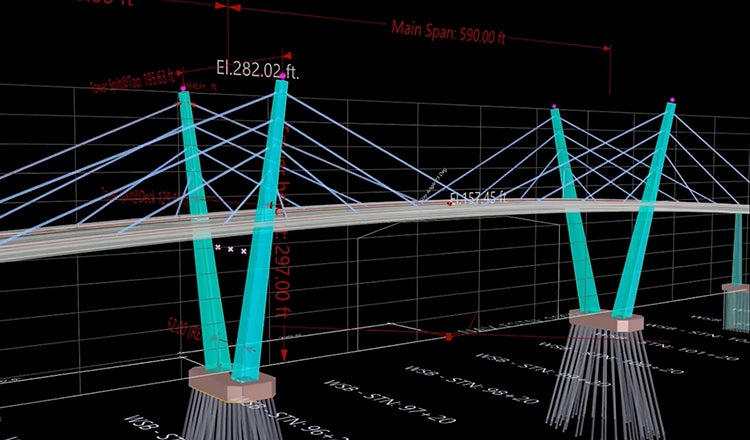
Q. How is this different from more traditional approaches to complex bridge design?
A. Conventional approaches limit the possibilities we can explore cost-effectively in a multi-dimensional design environment. Parametric design opens up the opportunity to explore more viable forms and leverage our expertise and client collaboration at a different scale, bringing new opportunities to flex our design muscles.
Signature bridges demand a totally different approach to conceptualizing and form-finding compared to simpler bridges, but they are still subject to the same codes and structural engineering rigour. Solving the design puzzle is hard on any budget and scope, and even harder on complex signature bridges where almost everything is unique. Parametric tools provide a platform to solve these challenges more effectively. Exploring options through parametric tools is the start of, and a strong visual case for, understanding that a design concept works in the real world.
A small pedestrian bridge with a unique shape suited to the neighbourhood may have a smaller design budget which requires the efficient modeling and vetting of numerous concepts and alignments over varied topography and site constraints — that’s a perfect application of parametric design. At the other end of the spectrum a signature bridge can be efficiently modeled and envisioned — for example, for tower shape, configuration and height on a cable-stayed bridge — so that parametric design reliably automates the detail work required to stay up-to-date when developing the signature bridge design.
The efficiency and technical rigour of a parametric design approach aligned with technical expertise improves solution finding and client engagement which opens up new design configurations for our bridge experts to develop that may have been challenging or impossible to manage/execute any other way.
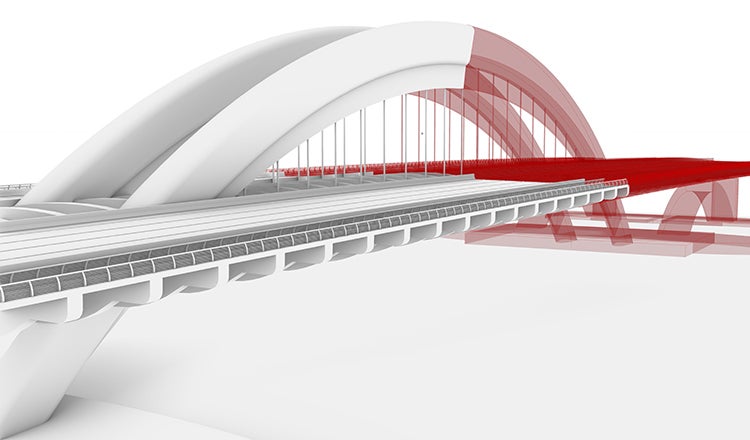
Inspiration and Advice
Q. What got you interested in parametric design?
A. I’ve always been captivated by the application of technology to engineering, be it computer programming or CAD applications. Since learning AutoCAD in eighth grade, it become evident to me how critical our drawing tools are, how they benefit an industry where geometry is the design, and how they benefit our ability to understand our design solutions better.
When I came across a design problem that required laying out and cutting flat plywood panels for a double curved surface, I struggled over the geometry and mathematics. A surveyor introduced me to Rhino3D and the Grasshopper plug-in; at first I thought it was cartoonish but, after seeing how easily it would unroll any shape to flat panels through mathematical articulation of the surface, I realized it’s a powerful evolution of CAD. I believe that these tools and way of designing are the most exciting and powerful change to our industry since CAD took over from vellum. These tools are the key to understanding structural form, function and design possibility.
Combining these tools with advances in industrial automation and artificial intelligence, I believe that parametric design is a doorway to the Fourth Industrial Revolution. Designers in other industries are stepping over the threshold and it’s up to structural engineers to capitalize on our expertise and knowledge to invigorate our role to lead bridge design into this next digital revolution with these innovative tools as well.
Q. What advice do you have for owners interested in adding parametric design to their toolbox?
A. Reach out to your local HDR project manager and request a demonstration specifically for your next bridge project. There’s nothing like seeing how this can work in your prospective project situation.
Public expectations for improved aesthetics in infrastructure are driving change away from cut-and-paste bridges. Owners often face challenges to meet these expectations under competitive budgets and constrained schedules. Parametric design streamlines workflows, iteration, and rework — especially on that non-linear spaghetti-interchange or ambitious architectural vision — thus improving quality and opportunities for unique design solutions. We spend less time re-iterating and reworking details and more time finding viable solutions for the public by seeing the bigger picture and overall fit.
Each Experts Talk interview illuminates a different aspect of transportation infrastructure planning, design and delivery. Check back often to see new insights from the specialized experts and thought leaders behind our award-winning, full service consulting practice.