
Doing More With Less: Designing to Maximize Value
How can we maximize budget value without compromising program or design ambitions in science and research facilities on academic campuses?
We came face-to-face with this question when we did a cost check on a new science building we were designing in the middle of the pandemic when our entire industry was facing increasing fuel cost, labour and material shortages, and a busy construction market. Our project was over budget by about 30%. From a cost-per-square-foot perspective, it was almost 14,000 square feet. Removing this much area would have put the feasibility of the building, with its aim of increasing research capacity on campus, in serious question.
Even more alarming, we started to notice this pattern in other education and science projects in a similar design phase. We needed to explore effective strategies to overcome the overruns without big compromises on the projects. We also needed to explore how we could anticipate these sorts of cost impacts in the future since higher costs are now holding. The client's budget and how we use it most effectively was front of mind for us. The typical value engineering approach led to unacceptable compromises. We realized that without some out-of-the-box thinking and reframing of the question, no solution clear was on the horizon. We would need "value design" instead of "value engineering" to overcome the battle of budget and value.
What Is Value Design?
Value Design is an approach that we've used on our integrated project delivery projects, but have been able to apply it using more traditional delivery methods as well. We've found it particularly helpful for designing complex science and research facilities with many competing requirements.
Defining Value
Value, in the context of project management, can be defined as the relationship between the function or results achieved and the cost incurred to achieve them. It is a measure of how much benefit or worth the project delivers compared to the resources invested in it. One way to increase value is to achieve the same performance at a lower cost; but there is a limit to how much you can lower the cost before compromising the function. However, cost reduction is not the only way to realize value and in no way guarantees true value; rather, realizing value is about optimizing the relationship between cost and benefit to achieve the desired results efficiently. Another way to create value is to maximize the results that are possible while keeping the cost fixed or even driving them down further.
Value Is More Than a Sum of Parts
When we think about value in the context of construction projects, we can break it down into components. The project is evaluated based on each budget component's value or what each discipline brings to the table.
On a typical science and research project, the construction budget structure is similar to the pie diagram below. As you see, the architecture (envelope and fit-out) is only 25% of the total construction whereas mechanical and electrical costs are around 40%. Therefore, it's impossible to value engineer the architectural scope enough to make up for the 30% budget overruns that the science projects are experiencing post-COVID!
To effectively address cost overruns at the time of budget crisis, each component should contribute to the savings pool proportionate to their share of the total construction budget — think about it like a taxing system.
Unlike how value engineering is commonly practiced, each component should contribute to the saving pool proportionate to its share of the total construction budget — like a tax mechanism.
A 30% budget overrun cannot be feasibly resolved in a science project by only reducing the area.
But the real value is when we can find synergies between project components so that a decision in a certain scope can bring benefits to other components as well. If we think outside of these silos, then the sum can be bigger than the parts. So, a value-driven approach focuses on maximizing the project's benefits while minimizing the cost incurred to achieve them. Only by prioritizing value over cost can we ensure we meet the expectations and provide tangible benefits while also being cost-effective.
Value Design vs. Value Engineering
General Electric invented value engineering during World War II. Because of the war, there were all kinds of raw materials and component shortages. To ensure the continuity of their production, the engineers at G.E. looked for acceptable alternative parts in the original design.
Over the years, value engineering has evolved to become a widely accepted approach to budget management. However, some critics argue that the focus on cost reduction can sometimes lead to a reduction in quality or functionality, which is why the value design approach has emerged as an alternative that prioritizes maximizing project value while staying within budget constraints.
Value engineering is a linear process of switching one product or solution with another, but Value Design is a non-linear and systematic design thinking to balance results and cost. The below diagram explores the relative cost of change over time in a construction project. Although there is always a cost associated with a change, it's much cheaper to make changes, consider options and optimize value at the beginning of the project. Later in the project, making change (especially reactive change in the form of value engineering) becomes expensive decreasing the overall value of the project.
Real-World Benefits of Value-Based Decisions
Back to the project we mentioned at the beginning, we tightened up the spaces with the users and saved some area. But the real savings came about when we committed to a “value design” approach. Here are a series of related decisions with a caveat that helps us realize cost-effective solutions for this specific project.
Decision 1 | Planning Efficiencies
The space program had a diverse range of spaces with vastly different requirements and adjacencies. To address this, we divided the program into three primary areas — wet (intense labs), damps (clinical research), and dry labs (offices and computational research).
To optimize the functionality of the space and flows, we made some strategic decisions early on.
For example, we decided to locate the wet labs on the lower level with direct access to loading, while the mechanical room was placed above the wet labs to save on interstitial space for maintenance. This one decision had several implications that we'll explore in more detail shortly.
Furthermore, we placed the faculty offices and graduate student spaces on the top floor, allowing for a more conducive research and learning environment. By thoughtfully organizing these spaces, we were able to meet the program's requirements AND maximize value.
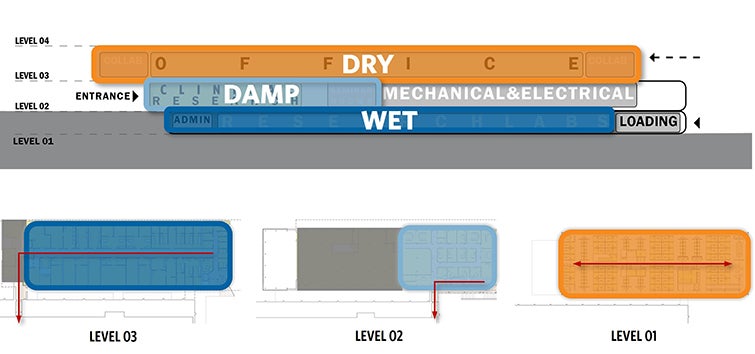
Decision 2 | Optimizing Mechanical Distribution
Locating the mechanical room above the wet labs helped us save on interstitial space. But this decision had other implications too — it led to a significant reduction in the mechanical and electrical distribution and shaft spaces compared to a typical roof penthouse scenario. This was a game-changer for the project, as it allowed us to optimize the available space while also reducing construction and maintenance costs.
Another advantage of this blocking strategy was that we could have a separate mechanical system for the dry lab spaces. As the labs were right above the mechanical room, we chose a ductless underfloor system, which further saved on the distribution system costs. The ductless underfloor distribution system allowed for greater user control, with adjustable diffusers and improved air quality and efficiency, thanks to the low-level supply and high-level exhaust.
Decision 3 | Hybrid Mass Timber Structure
The decision to locate the intense labs on the lower level within the concrete foundation structure freed us to be more creative with the superstructure on other floors. After careful consideration, we opted to use mass timber as the primary structural material, which had several positive implications for the project's cost and value.
One advantage of the exposed mass timber on the top floor was that it created a more welcoming and interesting workspace, which has been proven to boost productivity and user satisfaction. The exposed structure also helped us save on finishing costs, making it a more cost-effective option.
Moreover, the prefabricated nature of mass timber provides significant time-saving in the construction schedule, which helped us stay on track. And, finally, of course, mass timber is an incredibly environmentally friendly material, as it sequesters carbon rather than generating it. By selecting mass timber as the primary structural material, we were able to not only optimize the functionality and value of the space but also be cost-effective and sustainable.
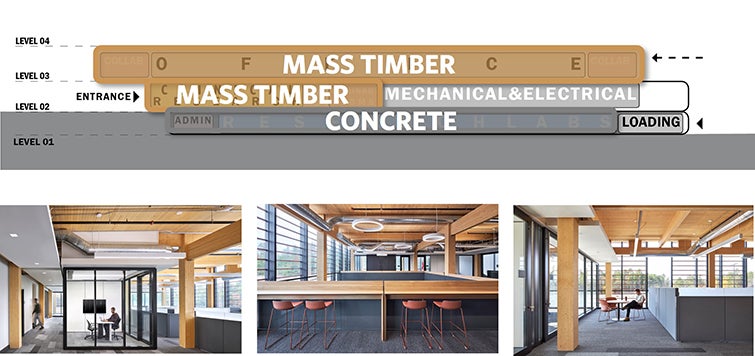
Decision 4 | Green Roof
One unexpected but welcome benefit of not having a mechanical penthouse on the roof was we could utilize our roof for stormwater management.
According to the local municipality, new buildings were required to have 40% green roof coverage at the time. However, we discovered that by covering the roof with pre-grown green roof modules, we could avoid long-term discharge to the city, simplifying the permitting process and reducing operational costs.
By adopting a value design approach and exploring optimized solutions like utilizing the roof for stormwater management, we were able to balance the functionality and value while meeting regulatory requirements and reducing operational costs.
Decision 5 | Fritted Glass
We initially considered fritted glass because of the requirements for bird-friendly frit. Then we realized a customized pattern with higher density on the west and south facades can minimize glare and heat gain. With the custom frit pattern, we also eliminated the internal blinds that are a maintenance hassle. This led to reducing mechanical load and downsizing AHUs, which resulted in significant cost-savings.
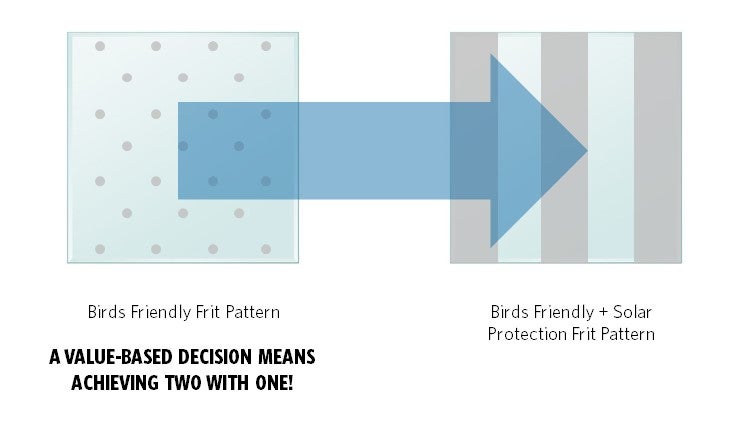
How Value-Based Decision-Making Can Be Implemented
In an “integrated delivery” model, the owner as well as the design and construction teams are set up to naturally work in a collaborative manner incentivized to increase the budget value. In traditional delivery methods, an “integrated design” methodology is the only way to promote value-based decision-making. We were fortunate with a client that trusted us and encouraged the team to think long-term and out-of-the-box.
This article is part one of a trilogy on managing budget without program compromises on education and science projects. Stay tuned for more on the science trends that impact cost and how you can take advantage of them to increase value; as well as value-conscious tools we can borrow from Integrated Project Delivery to implement in other deliveries to better balance costs and benefits.