
Make a Data-Driven Water-Use Plan for Your Power Plant
Use data from studies and models to inform your long-term water management plan
Optimizing your power plant's water use starts with understanding your plant's current water picture and associated costs. Next it's about identifying opportunities for conservation, minimization and reuse or recycling. The ultimate goal is to manage the plant's water resources in the most efficient manner. Whether your driver is achieving compliance with new regulations, minimizing operating costs, taking a more sustainable operations approach, or a combination of these factors, tools such as interactive water balance modeling and conservation studies narrow the options and identify optimal, cost-effective options for implementation.
Conduct a Water Conservation Study
Finding opportunities to reuse, recycle and reduce water consumption and discharge may seem obvious, but these types of solutions are frequently overlooked when the quality of various sources isn't readily understood. Often a minor change to a chemical treatment program or other operational change can allow for reuse of a wastewater stream that was previously considered not recyclable. A water conservation study can help identify these opportunities to eliminate waste and maximize efficiency for the long term. By conserving water, your plant may realize cost savings and build good will with your neighbors for employing a more sustainable approach.
For example in Wisconsin, the Department of Natural Resources requested that our client develop a water conservation plan encompassing two of their plants. We worked with them to develop plans now and into the future to conserve and recycle water at each station.
The plan was the first of its kind for a power generating facility in Wisconsin. In order to be good stewards to the neighboring community, sustainability was a big focus throughout the development of the project.
Compare Options with an Interactive Water Balance Model
A water balance model should be an interactive tool designed to enable you to evaluate multiple opportunities for water optimization using a customized set of data. It's not as simple as a picture of boxes with directional arrows and flow rates — an interactive water balance model looks at real costs, actual water quality data, actual chemical consumptions, real flows and real equipment in your facility.
How does the water balance model work?
The water balance utilizes data from the plant's initial design, distributed control or plant information system, to obtain flow and chemistry information. Combined with user-entered cost and chemistry data, the water balance provides a continuous update of the cost of water system operation. Once completed the water balance can be used to model and estimate the cost of any operational or mechanical changes, create budgets, evaluate bids, identify process bottlenecks and create process improvements. Using a modular format, you can evaluate hundreds of possible scenarios quickly and accurately.
A customized interactive water balance model is a sophisticated, cost-effective way to gain a wealth of information for decision making. Creating a plant water balance gives you the opportunity to compare different operating scenarios beyond a simplistic line item with flow rates-and assess associated operating costs. For each option, you can adjust factors including chemistry and flow rates, and view operating cost at any specific point in time or over any period of time for the entire water treatment system or for any individual component.
One of the greatest benefits of modeling scenarios is your ability to clearly show where water and cost savings originate. It's empirical evidence of your proposed solution, and how it'll affect operations.
Modeling Makes an Impact at a Power Plant
A power plant in the West had a complicated brine recovery system. Operators reported that the softeners took an extremely long time to "rinse in" and produce hardness low enough for feed to the reverse osmosis units. Our team developed a water, mass, chemistry and cost model of their entire plant to pinpoint the underlying issues with a goal to optimize plant water usage.
Through the model, we found a chemical underfeed that resulted in only partial regeneration of the softeners and extremely long rinse times. The long rinse times created problems with the plant water balance. Since the reverse osmosis units couldn't operate without low-hardness feedwater, the long rinse times created a problem with accumulating brine that couldn't be recovered.
After making the changes in the model, the client realized significant benefits:
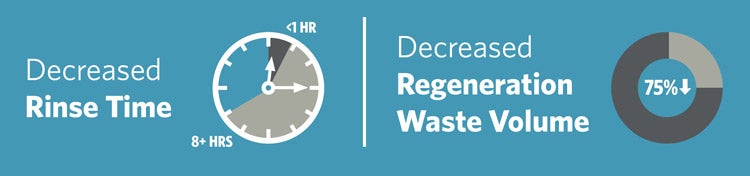
Identifying the best opportunity for optimizing your plant's water use will set you up for a cost-effective long-term solution. It's critical to use tools that generate reliable data to gain support from decision-makers and stakeholders.