
Considerations for Installing Gypsum Board in Cleanrooms
Gypsum board offers an alternative to prefabricated panels in some life science cleanroom applications.
Science research facilities are increasingly considering sterile environments called cleanrooms for research and manufacturing. Cleanrooms provide a sterile, clean space that reduces the chance of contamination in manufacturing facilities for pharmaceutical or semiconductor devices and creates appropriate aseptic conditions for research activities that are sensitive to air quality or particulate matter. Cleanrooms have stringent air quality requirements, built from construction materials with resistance to decay over time or low friability, thereby reducing particulate generation and aerosols.
Although common in physical sciences research and pharmaceutical manufacturing, cleanrooms are also used for life sciences research. In life science research, aseptic environments are required to carry out cell therapy, gene-modified cell therapy, tissue engineering, imaging and photosensitive work.
Due to the complexity with the design and construction of cleanrooms, there is a proclivity for design and client teams to delegate design and construction of these spaces to a cleanroom vendor contractor. When this happens, the quality and cost factors are often left in the hands of the cleanroom vendor contractor. However, in cleanroom construction, the selection of materials are an important consideration in order for the design and construction team to achieve desired quality.
Frequently cleanroom vendor contractors, irrespective of the cleanroom class, use prefabricated panels manufactured by them or by preselected suppliers. While prefabricated panels can help achieve any level of cleanliness, they can be unwarranted for cleanrooms classes of ISO 7 and ISO 8, especially in life science research facilities. Also, prefabricated panels come with limitations in functionality and can be cost-prohibitive.
For cleanroom spaces that are unclassified or with ISO 7 and ISO 8 class rating, gypsum board products can be a suitable alternate as they have significant benefits. However, gypsum board products are not recommended for cleanrooms in semiconductor manufacturing or microelectronics facilities and spaces with ISO 6 or higher class ratings.
This article elucidates the advantages of using gypsum board over prefabricated panels for cleanroom construction and differences between them. It also provides some design considerations for a design team looking to implement gypsum board for cleanroom construction.
Cleanroom Materials and Installation Methods
The most popular material for cleanroom shell structures is prefabricated panels. Prefabricated panels are made of bonded resin, sandwich aluminum panels, honeycomb core aluminum, aluminum framed uPVC, glass reinforced plastic and high-pressure laminates. Cleanroom panels of modular sizes fabricated from aluminum honeycomb panels are used extensively in electronics, semiconductor manufacturing or precision physical sciences research spaces.
Prefabricated panels have limitations with functionality. These panels typically require a backup structure, can easily get dinged in high traffic areas with frequent cart movements and do not offer fire-rating. Walls faced with gypsum board wall construction offer durable wall surfaces in such high traffic areas. If a project requires fire separation or compartmentalization between cleanroom suites, then using gypsum board walls as the primary barrier or a backup to prefabricated furring panel is a solution. Joints between prefabricated panels are not desirable, which are eliminated in gypsum board drywall construction.
Gypsum board products offer cost benefits, are more readily available, are more customizable and are easier to procure compared to prefabricated panels. Building trades and manpower are not a constraint as it is common trade. Using gypsum board also offer shorter lead times than prefabricated materials.
ISO 7 and ISO 8 class cleanrooms are quite common in life science research environments and aseptic formulation spaces. Hence, gypsum board have extensive potential for application. As noted, before, not all cleanrooms can be built using gypsum board products. They are not recommended in large rooms with high volume of air movement and in manufacturing facilities for semiconductor or microelectronics. Also, prefabricated panels will continue to be preferred in tenant improvement projects or fit outs, because mitigation measures for dust generation from gypsum board products can be challenging with adjacent occupied spaces within existing buildings.
As an additional consideration, gypsum board should only be used in single-phase new construction since concerns with particulate contamination of HVAC systems can be handled better as a larger construction area can be brought under control within the cleanroom construction zone, which is not the case in multi-phased construction projects.
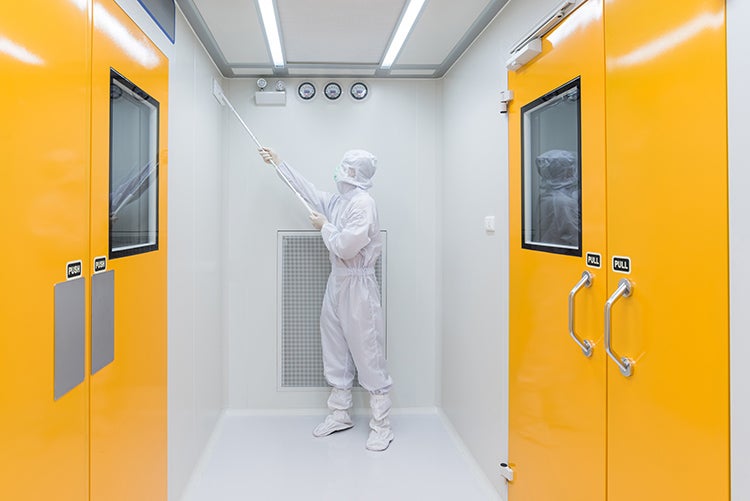
Gypsum Board Design Features in Cleanroom Construction
When planning and designing a cleanroom, there are plenty of aspects to account for such as air quality, personnel and material flow, mitigation measures for dust, HVAC systems, cleaning procedures, windows and more. In addition, there are also specific design features to account for when implementing gypsum board products in cleanrooms.
Wall selection: Use gypsum board drywall in the unclassified high traffic corridors areas and technical equipment rooms even if prefabricated cleanroom panels are used in the interior of cleanroom suites. For cleanroom walls bordering a corridor/ unclassified space and without air return chases, use a cleanroom panel furring installed over a gypsum board wall with the furring facing the cleanroom side.
Wall and Ceiling Finish Coatings: Cleanroom walls and ceilings using gypsum board should be finished with fiberglass, thermoplastic sheeting. Alternatively, an applied epoxy coating and finish coating using three-part epoxy should be specified for all surfaces exposed in the clean area. These spaces also need to be adequately flushed during and after construction to remove VOC off-gas.
Wall and Ceiling Details: Gypsum wall and ceiling details need to include a coved base and coved ceiling corners to provide ease with surface cleaning. Ledges need to be sloped and offsets eliminated on vertical wall surfaces as well.
Sealants & Epoxy Finishes: Sealants need to be used to close gaps and crevices between surfaces and high-build epoxy needs to be included in floor finishes. Additionally, painted doors, windows and frames should use an epoxy-based paint system.
Construction Considerations for Gypsum Board in Cleanrooms
When constructing a cleanroom with gypsum board, there are important external considerations to factor in:
- A high degree of supervision during construction is needed to maintain air quality by keeping a low particulate count.
- Daily, monthly or weekly reporting of log sheets of construction in clean zones should be made part of closeout submittals.
- Mandatory experience in cleanroom construction should be included in contractor bidding.
- Design teams need to consider if construction teams have prior experience with the protocols of cleanroom construction and discuss with the construction manager and client while preparing construction documents and specifications.
- Division 1 specification should cover cleanroom construction protocols and procedures based on the recommendation of ISO.
- The design team should include in their Division 1 specifications a quality assurance program requiring contractors to document the construction progress aimed at monitoring cleanliness at every stage
In conclusion, gypsum board can offer many benefits for cleanroom design when implemented for ISO 7 and ISO 8 rated classes, particularly for life science research applications. When implemented, it’s important to work with designers and consultants that have a good understanding of the extra considerations for design and construction to realize the benefits in cost saving and meet the expected performance.