
Revolutionizing Solar Piles and Reducing Cost with One Simple Innovation
Our idea is pretty simple: subtract one pound of steel per foot length from every pile used to support a solar photovoltaic panel. The impact? Significant. Photovoltaic facilities average 500 steel piles per megawatt, and projects with more than 100,000 steel piles aren’t uncommon. That pound of steel quickly adds up to cost savings of hundreds of thousands of dollars. Not to mention an added bonus of flexibility.
Pile optimization, which involves changing the way photovoltaic ground mount piles are designed, came out of brainstorming ideas with Paul Sehrt at PACO Steel. Initially our goal was value engineering on a client’s behalf, but we quickly realized a shift in the standard approach to solar pile design would bring measurable benefits to this client, and many others.
How it Works
Traditional solar piles offer six steel pile sizes to choose from. If one size isn’t strong enough to support the load, the engineer selects from the remaining options and copies the design tens of thousands of times. It’s safe, and per the building code — but solar projects are sensitive to cost. Since the same pieces are replicated over and over, extra steel here and there adds up to a lot.
Pile optimization places the steel within the pile where it best resists the loading, which minimizes the amount of steel required. Because the piles are customized they provide same level of support, and are designed per building code requirements.
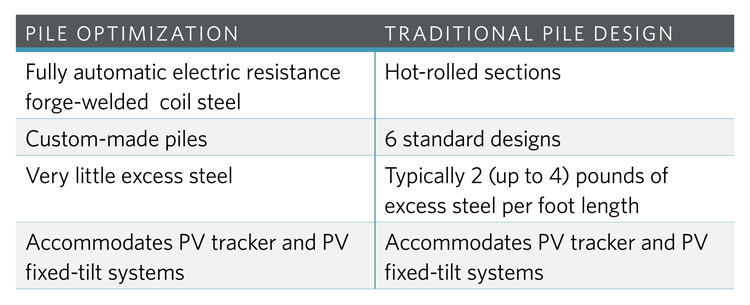
An Exciting Domino Effect
As we’ve seen pile optimization come to life, the impact of our idea has come full circle. Steel weight savings on five pilot projects ranged from 10 to 25 percent, with steel tonnage cut by 200,000 to more than a million pounds compared to standard hot-rolled steel pile sections.
Galvanizing costs are reduced because galvanizing is based on pounds of steel and not number of piles. Reducing steel weight enables a greater number of piles on a truck, which means fewer trucks needed for shipping. Less galvanizing, which uses zinc, and fewer trucks on the road help reduce the project’s carbon footprint.
It’s been fun to see our idea come full circle, and help clients do more with their dollars. Some have reinvested their savings to fund additional solar photovoltaic panels or other areas of their facilities. Others have used it to help support the cost of additional projects.
What would you do with a few hundred thousand dollars to reinvest in your venture?
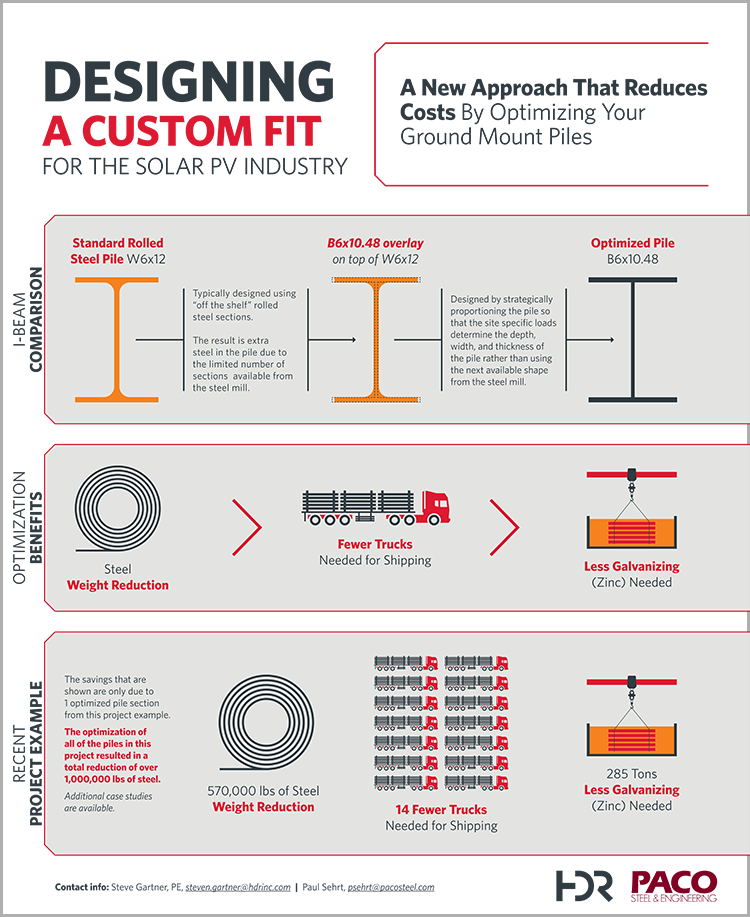