
Building the Container Terminal of the Future
How Collaboration and Teamwork Laid the Foundation for Successful Program Strategies on the Hugh K. Leatherman Terminal in North Charleston, SC
By Andrew Thiess and Frank Proctor
The Hugh K. Leatherman Terminal in North Charleston, South Carolina, opened its first phase in March 2021. The first container terminal to open in the U.S. since 2009, the project includes a new 1,400-foot berth and a yard that can accommodate a throughput of 700,000 twenty-foot equivalent container units annually. This added TEU capacity will help ensure the Port of Charleston remains one of the top 10 in the U.S. in container volume.
HDR has provided construction management, quality assurance and design review services for the project since 2017, working around challenging site conditions, waterways, motorists and even possible unexploded ordnance from World War II training sites to deliver millions of dollars in savings for the South Carolina Ports Authority.
Many efforts contributed to the immediate success as the first phase opens, including an owner with a clear vision of its needs and priorities and a collaborative spirit that encouraged innovation. But some strategies stand out:
- A design and contracting strategy that prioritized local participation
- Value engineering at the beginning of the construction process that discovered tens of millions of dollars in savings
- A risk management process that anticipated and proactively managed obstacles
The common thread in all was a shared mindset of collaboration and collective goals. The sense of teamwork maintained throughout the project led to better outcomes and a common interest in success. As on any project, there were ups and downs, but everyone was pulling in the same direction with a good attitude, and that led to a winning result in the end.
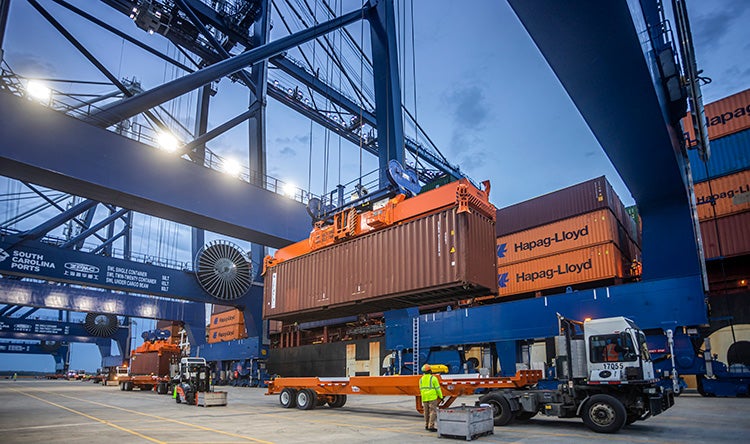
Multiple Contracts to Maximize Local Participation
When the terminal project began, it was envisioned as one contract. That is a viable strategy in many instances, particularly in locations where local expertise is lacking or already committed to other projects. But for this project, our team felt it was better to break the project into multiple contracts that could be fulfilled by local contractors to benefit from their expertise.
Rather than one large contract, the terminal was broken into five discipline-based contracts:
- Wharf
- Site work
- Two bridges (one contract each)
- Buildings and canopies
This contracting strategy paid big dividends when it came to flexibility and trust. It allowed the team to work with local companies on value engineering proposals and proceed with construction in a flexible, open relationship that prioritized the best interests of SC Ports. With the majority of the contracts filled by local contractors, team members were invested in the community and motivated to maintain a good relationship with SC Ports. That meant a combined team that went the extra mile to meet SC Ports’ goal of opening the terminal on time and within budget.
A good working relationship built over time between the owner, engineer and contractors also contributed to the success. As the projects commenced and contractors realized the owner and owner’s engineer were fair and reasonable, the contractors were far more reasonable on change order pricing and the sharing of costs and risks. This positive relationship, with mutual trust, ultimately benefited SC Ports, who came to rely on all parties to deliver services at lower cost.
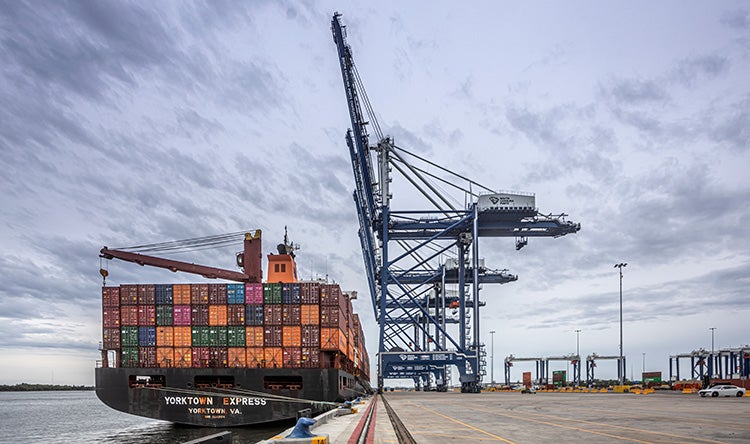
Identifying Cost Savings Through Value Engineering
Value engineering became very important when initial bids on some contracts exceeded the engineer’s estimates by 20% or more. Faced with a strict budget limit, savings had to be found. Identifying these cost savings happened in multiple value engineering workshops that included SC Ports, HDR and contractors working together to develop and vet ideas. Many ideas were incorporated into the final design, while others were determined not viable or simply did not provide SC Ports with sufficient value to warrant adoption. In the end, the process saved nearly $32 million across multiple contracts.
The major areas of savings eventually identified and executed included:
- Precast construction of wharf and optimization of revetment: $8.4 million savings
- General conditions, bid clarifications, and price cuts: $4.2 million savings
- Complete redesign of site pavement, drainage and utilities: $7.2 million savings
- Optimization of lighting and electrical systems: $5.1 million savings
- Redesign of water distribution system, removing unnecessary pump station: $1.1 million savings
- Simplified maintenance building: $6.2 million savings
Each of these value engineering alternatives involved re-design while construction contracts were underway. This involved a tremendous amount of coordination, flexibility and patience as construction was being accomplished in parallel with future design development. In the end, the teams were able to deliver and open the terminal below budget and ahead of the March 31, 2021 terminal opening target date.
What is more, the synergy of the engineering and construction teams allowed SC Ports to incorporate additional features into the project. A full commercial kitchen was designed and built in the new terminal operations building; and a temporary chassis yard was added to the terminal; all within the original contract time frame, though neither were in the original scope of the job.
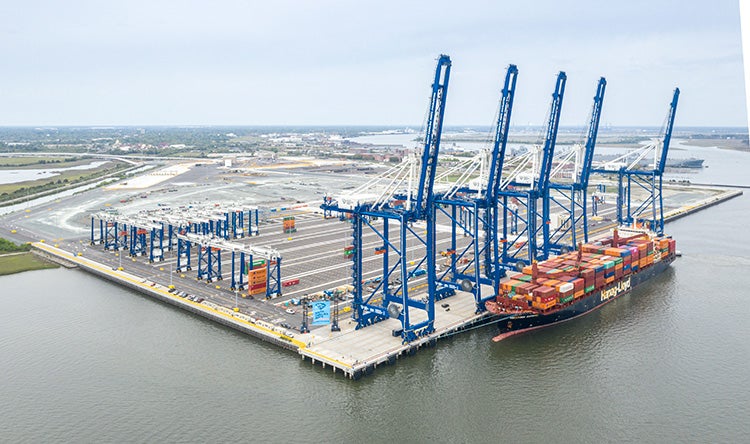
Reducing Unexpected Impacts Through Risk Management
Like any major project, the team had to anticipate and mitigate many risks that threatened to disrupt schedules and budgets. Once value engineering was done, a proactive risk management process helped keep the program on track throughout construction.
A program-level schedule coordinated work between various contractors. With five concurrent contracts, hundreds of workers and dozens of subcontractors, were all working at any time within a limited footprint. Regular and frequent coordination and progress meetings, including contractors and key subcontractors, ensured that all parties working to complete the project were on the same page, reducing delays.
Numerous risks were identified and anticipated. One key risk was the site conditions. The container terminal was built on highly compressible material and a former dredge disposal area that is expected to continue to settle up to one foot over the next 25 years. Knowing this was an issue, our team insisted that designers incorporate flexible or telescoping utility connections to all pile-supported buildings and structures. Flexible connections mean that as the ground settles around structures, the pipes, electrical lines and other connections will expand and won’t be damaged.
The time it would take to install nearly 10 miles of electrical duct banks with over 125 miles of electrical conduit on a site with a very shallow water table and a very shallow network of storm drain pipes was also a major concern going into the job. The engineers and contractors reconfigured the duct banks to minimize depth and allow them to be installed above the other utilities. Spreading the conduits out (up to 10 wide) and limiting the height to two conduits precluded the need for the much deeper and time-consuming excavations originally specified.
Another significant challenge faced by the team was maintaining access for local traffic to a nearby marina. This was a critical objective as the original road was completely cut off by the installation of new bridges. HDR developed an alternate design to divert but maintain? traffic around the work site, avoiding a multitude of safety and coordination issues.
HDR also foresaw the need for the wicking and surcharge of the backland area behind the Phase 2 wharf. This was a key to getting the next berth constructed in a timely and efficient manner. With all of the necessary expertise already on site, it was a simple matter to expedite this critical work and shave many months off SC Ports’ overall development schedule.
Expertise and experience in terminal construction were vital components of managing risks. Previous experience of HDR’s project leaders on other terminal projects meant that we could anticipate problems before they arose, particularly important when working with contractors and others who haven’t previously built a container terminal.
Having done this before and having seen projects struggle at certain milestones, we have a better sense of where the risks are and how long processes take, whether installing 125 miles of underground conduit or managing security infrastructure. That understanding helped us work with our clients to plan ahead and address concerns before they became critical.
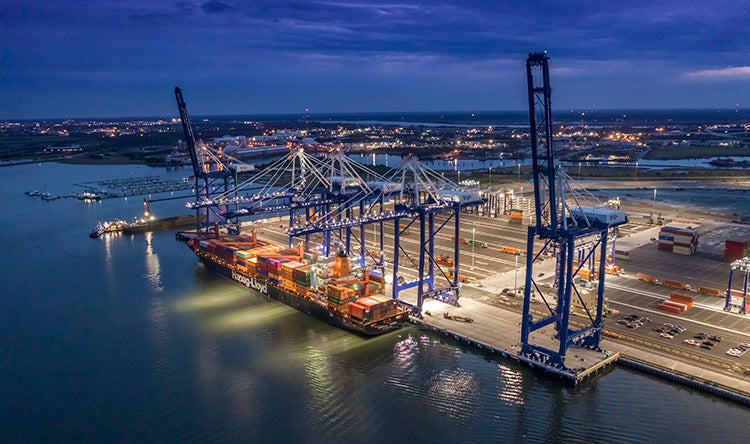
Success Built on Collaboration
The Hugh K. Leatherman Terminal welcomed its first container on March 30, 2021, followed by its first vessel on April 9, the culmination of an effort decades in the making. Marking the occasion, the SC Ports team repeatedly pointed to collaboration as a key element in the project’s successful completion.
“The complexities of building a container terminal require great teamwork and persistence over many years,” said Butch Weber, SC Ports’ general manager of project management and construction.
“The SC Ports team and our project partners made the decision to collaborate daily, resulting in creative, value-added designs for this critical project,” said Lucy Terza, SC Ports’ engineering project manager.
“The level of coordination exhibited by all of the project partners was the best I’ve seen in my nearly 40-year career,” said Walter Lagarenne, SC Ports’ senior director of engineering and facilities.
Opening on schedule and within SC Ports’ budget on such a major project began with developing the right contracting strategy, was helped along through value engineering efforts and guided by a risk management strategy that kept the project on track. But ultimately it required a dedication to collaboration from every team member invested in delivering the best project possible for South Carolina.
About the Authors
Andrew Thiess is a senior project manager with over 30 years of experience in construction management, engineering design, project management, business development, feasibility studies and planning of major industrial projects both in the U.S. and internationally.
Frank Proctor, our ports and maritime technical director, has more than 25 years of experience in the planning, design, and management of cargo terminal development projects (including container, bulk, liquid bulk, and Ro-Ro facilities) for public and private clients. He is an experienced manager of complex multi-disciplinary industrial marine facilities projects.