
Getting Ahead of Lead
Taking a Proactive Approach to LCR Compliance
With a 20-year track record of testing below the Lead and Copper Rule’s lead action levels, it may seem Tacoma Water had no reason to invest in lead control strategies. But lead-related water quality events at Flint, Michigan prompted the utility to re-examine its LCR compliance activities and reaffirm its commitment to further reduce drinking water lead exposure for its direct and wholesale customers. Tacoma Water also had its eyes on the recently published LCR revisions and the challenges those revisions may bring. For these reasons, the utility took proactive steps to re-examine its LCR compliance activities and develop concrete steps to maintain customer safety.
Getting an Early Start
Tacoma Water is one of the largest utilities in the Pacific Northwest. Surface water from the 150-million gallon per day Green River Filtration Facility is its primary source, with supplemental groundwater supply from the 45-MGD South Tacoma Wellfield and additional outlying wells. Its distribution system has never had lead service lines, but large portions of its housing stock was developed with lead goosenecks, copper plumbing with lead/tin solder, and leaded brass meters and faucets. Lead concentrations have been below the regulatory 90th percentile action level of 15 µg/L in its LCR sampling data since 1997 when corrosion control treatment was installed on the Green River supply. However, Tacoma Water did see higher lead corrosion rates with a 90th percentile lead concentration of 14 µg/L as late as 2010. To reduce public health exposure to lead, the utility systematically identified and removed all the lead goosenecks throughout its system, a process that was completed in 2021. In addition, Tacoma Water implemented corrosion control treatment at the South Tacoma Wellfield in 2013.
Keeping the Momentum
HDR partnered with Tacoma Water to help guide the next effort: evaluating its current corrosion control processes. One key factor in this was the blending of a variety of water qualities. While the utility’s major supplies have corrosion control treatment, many of the smaller groundwater supplies currently do not. Though used infrequently, these supplies serve a variety of purposes, such as meeting demands when the river supply is not available or is at reduced capacity due to high turbidities; during droughts; for emergency responses; and to balance water supplies within the regional transmission and distribution system. Further, optimal water quality parameters had not been developed previously for the South Tacoma Wellfield, even though it already has corrosion control treatment, so this was an important piece of the study.
To help identify the most cost-effective path forward, our approach followed these four steps.

Step 1 | Review historical water quality data: To identify trends that could further reduce lead corrosion, we started our evaluation by reviewing background literature and historical data related to LCR compliance. We also reviewed operational practices over a 10-year time period to acquire more insight into the current pattern of lead release in Tacoma Water’s system. Due to the system size, the varying water sources used and the multiple changes that Tacoma Water has implemented over the years, this was a key step in the corrosion control assessment.
Our data review evaluated the impacts from operational practices/changes, system pH, system chlorine residual and source of supply on LCR compliance.
Step 2 | Conduct pipe loop study: After the water quality review, a pilot pipe loop study was performed to further understand the fundamental interactions between Tacoma Water’s water qualities and copper piping, lead goosenecks and brass meters and valving that could cause lead and copper release into customers’ water. Test rigs were assembled at three locations in the distribution system with one of each of the three testing components (copper pipe, lead gooseneck and brass meter and valving) directly harvested from homes in Tacoma Water’s service area. Figure 2 shows a schematic of the typical pilot loop test rig. Specific test rig configurations varied to accommodate water supply and space constraints at each test location. Figure 3 is a photo of one of these rigs.
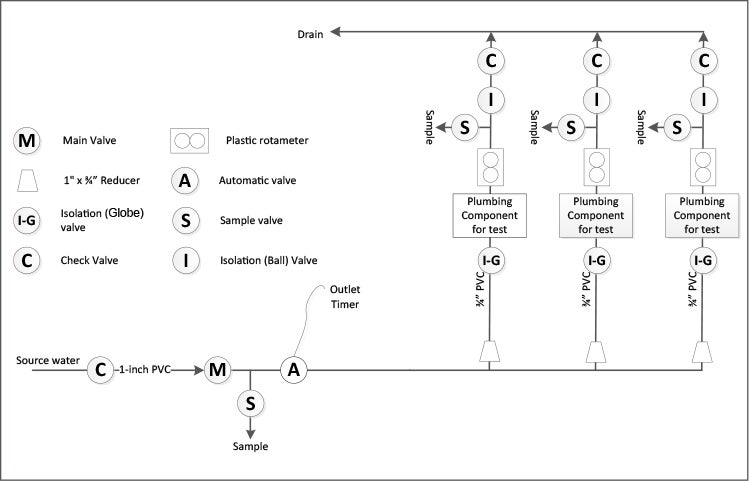
These test rigs were operated for seven months under conditions of 100% surface water, 100% groundwater and various surface/groundwater blends that Tacoma Water uses in its system. The testing quantified corrosion rates immediately after each water supply change and as the surfaces re-equilibrated to the water before another water supply change.
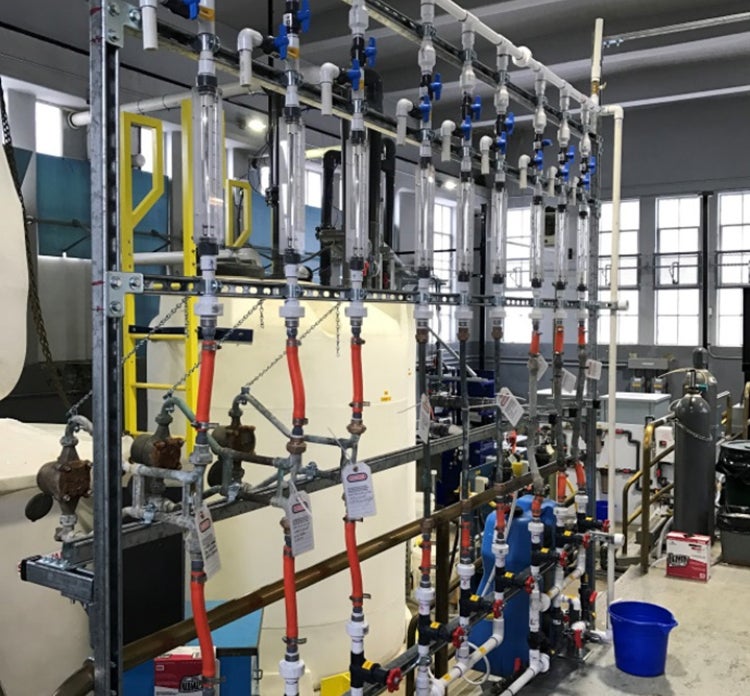
Test components were removed from the rigs on a regular basis for scale analysis at the University of Washington to provide insight into scale morphology and transformation as shown in Figure 4.
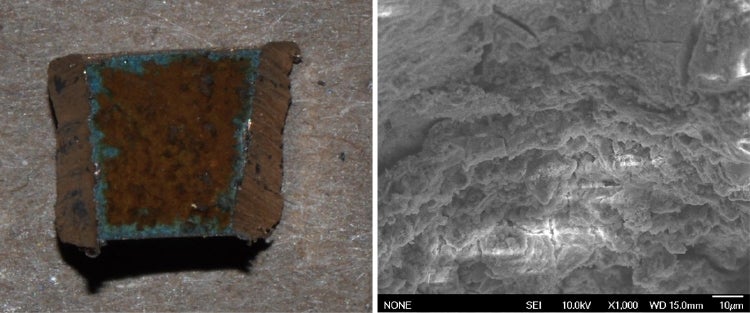
Step 3 | Develop water quality setpoints: Following the data review and pipe loop study analysis, we developed water quality setpoint recommendations to help achieve optimal corrosion control treatment throughout Tacoma Water’s system. The recommendations were developed to consider the current regulatory requirements as well as future revisions focused on minimizing lead release. These setpoints built upon the decades of work that Tacoma Water had already invested to minimize lead corrosion and reduce the impact of surface water/groundwater blending in its distribution system.
Step 4 | Quantify construction and operating costs: Finally, our evaluation reviewed all of the utility’s water supplies to determine the magnitude of chemical dosages needed to meet the setpoints. We developed conceptual improvement plans for those facilities that were found unable to meet the setpoints with existing equipment. Improvements included new chemical systems and buildings for the addition of sodium hydroxide to raise pH levels along with upgrades to associated electrical systems and instrumentation and controls. We used these conceptual plans to prepare budgetary-level capital and operational costs for the utility to use in capital planning.
Summary
Tacoma Water’s proactive approach to understanding and limiting corrosion throughout its system is paying dividends. Removing all lead goosenecks throughout its system, combined with over two decades of continued improvements in water quality, has resulted in a 90th percentile lead concentration of non-detect in 2019’s round of LCR compliance sampling — Tacoma Water’s lowest and best results ever. From these recent studies, the utility is further equipped with an in-depth understanding of its system, its resulting water quality parameters and information to use for capital improvement planning. By getting ahead of lead, Tacoma Water is well-positioned to successfully reduce public exposure to lead and address any challenges the LCR revisions may bring.
Authors:
Kim DeFolo, P.E., Principal Engineer, Tacoma Water, Tacoma, WA
Craig Downs, P.E., Assistant Division Manager, Tacoma Water, Tacoma, WA
Pierre Kwan, P.E., Water Treatment Technical Director, HDR, Seattle, WA